Trong lĩnh vực gia công kim loại tấm, xử lý bề mặt không chỉ ảnh hưởng đến vẻ ngoài của sản phẩm mà còn liên quan trực tiếp đến độ bền, chức năng và khả năng cạnh tranh trên thị trường. Cho dù được áp dụng cho thiết bị công nghiệp, sản xuất ô tô hay thiết bị điện tử, các quy trình xử lý bề mặt chất lượng cao có thể cải thiện đáng kể chất lượng sản phẩm và giá trị gia tăng. 10 mẹo chính sau đây được thiết kế để giúp bạn tối ưu hóa quy trình xử lý bề mặt kim loại tấm và giúp đạt được kết quả tuyệt vời một cách hiệu quả hơn.
Mẹo 1: Xử lý trước chính xác
Trước khi bắt đầu bất kỳ quy trình xử lý bề mặt nào, việc xử lý bề mặt kỹ lưỡng là cơ sở để đảm bảo hiệu quả của các quy trình xử lý tiếp theo.
Loại bỏ dầu bề mặt, oxit và rỉ sét là nhiệm vụ đầu tiên. Bạn có thể sử dụng chất tẩy dầu mỡ chuyên nghiệp hoặc chất tẩy rỉ sét, kết hợp với ngâm, phun hoặc lau bằng tay.
Đối với vết bẩn cứng đầu, có thể sử dụng phương pháp mài cơ học (như giấy nhám, đá mài, v.v.).
Chú ý khi vận hành:kiểm soát lực để tránh làm hỏng bề mặt nền, đặc biệt đối với các bộ phận kim loại tấm mỏng hơn.
Đề xuất cải tiến: Sử dụng thiết bị xử lý sơ bộ tự động (như hệ thống phun) để đảm bảo hiệu quả và tính đồng nhất của quá trình xử lý, đặc biệt là trong sản xuất hàng loạt.
Mẹo 2: Chọn vật liệu phủ phù hợp
Các tình huống sử dụng khác nhau có các yêu cầu khác nhau đối với vật liệu phủ của các bộ phận kim loại tấm:
Môi trường ngoài trời: Nên sử dụng lớp phủ có khả năng chống chịu thời tiết cao như lớp phủ fluorocarbon hoặc lớp phủ acrylic.
Các bộ phận có độ ma sát cao: Nên phủ lớp polyurethane hoặc lớp phủ gốm để tăng khả năng chống mài mòn.
Đồng thời, cũng cần chú ý đến độ bám dính của lớp phủ, có thể cải thiện bằng lớp sơn lót. Đối với các tình huống nhu cầu đặc biệt (như bề mặt kháng khuẩn hoặc cách điện), có thể cân nhắc đến lớp phủ chức năng.
Mẹo:Tính thân thiện với môi trường và hàm lượng VOC (hợp chất hữu cơ dễ bay hơi) thấp của vật liệu phủ đang trở thành xu hướng thị trường và lớp phủ xanh, thân thiện với môi trường đang được ưa chuộng.
Mẹo 3: Tối ưu hóa các thông số quy trình phun
Các thông số của quy trình phun quyết định trực tiếp đến chất lượng và hình thức của lớp phủ:
Khoảng cách giữa súng phun và súng phun: Nên giữ khoảng cách từ 15-25 cm để tránh tình trạng chảy xệ hoặc các hạt thô.
Áp suất phun: Nên sử dụng ở mức 0,3-0,6 MPa để đảm bảo sơn được phun đều.
Tốc độ và góc phun: Đối với các phôi có hình dạng phức tạp, hãy điều chỉnh góc của súng phun để đảm bảo lớp phủ được phủ đều trên các cạnh và rãnh.
Đề xuất cải tiến:Tiến hành các thí nghiệm phủ mẫu trong giai đoạn xác minh quy trình để tối ưu hóa cài đặt thông số và đảm bảo tính ổn định trong sản xuất quy mô lớn.
Mẹo 4: Sử dụng công nghệ phun tĩnh điện
Phun tĩnh điện đã trở thành sự lựa chọn hàng đầu cho xử lý bề mặt hiện đại do tỷ lệ bám dính cao và tính đồng nhất:
Hiệu ứng tiếp địa là yếu tố then chốt quyết định chất lượng phun và cần sử dụng thiết bị tiếp địa chuyên nghiệp để đảm bảo trường điện ổn định.
Điều chỉnh điện áp tĩnh điện theo độ phức tạp của tấm kim loại, thường được kiểm soát trong khoảng 50-80 KV.
Đối với các phôi phức tạp có lỗ mù hoặc khoang bên trong, có thể sử dụng hệ thống súng phun kép hoặc phun thủ công để tránh các khu vực lớp phủ yếu do hiệu ứng che chắn điện trường gây ra.
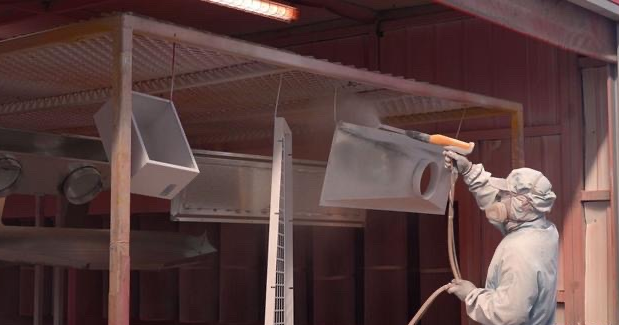
Mẹo 5: Xử lý phosphat hóa tăng cường hiệu suất chống ăn mòn
Xử lý phosphat không chỉ có thể cải thiện khả năng chống ăn mòn của chất nền mà còn tăng cường độ bám dính của các lớp phủ tiếp theo:
Kiểm soát nhiệt độ: Nhiệt độ phosphat hóa khuyến nghị cho thép là từ 50-70℃. Quá cao hoặc quá thấp sẽ ảnh hưởng đến tính đồng nhất của màng phosphat hóa.
Cài đặt thời gian: Thông thường là 3-10 phút, có thể điều chỉnh theo yêu cầu của vật liệu và quy trình.
Đề xuất nâng cấp: Sử dụng công nghệ phosphat hóa nhiệt độ thấp để giảm tiêu thụ năng lượng và kết hợp với dung dịch phosphat hóa thân thiện với môi trường để giảm áp lực xử lý nước thải công nghiệp.
Mẹo 6: Nắm vững những điểm cốt lõi của quy trình mạ điện
Mạ điện có thể mang lại tính chất trang trí và bảo vệ tuyệt vời, nhưng đòi hỏi phải kiểm soát quy trình một cách chính xác cao:
Mật độ dòng điện và nhiệt độ phải phù hợp chặt chẽ. Ví dụ, khi mạ kẽm, nhiệt độ phải nằm trong khoảng 20-30℃ và mật độ dòng điện phải duy trì ở mức 2-4 A/dm².
Nồng độ phụ gia trong dung dịch mạ điện phải được theo dõi thường xuyên để đảm bảo độ mịn và mật độ của lớp phủ.
Lưu ý: Việc vệ sinh sau khi mạ điện là rất quan trọng. Dung dịch mạ điện còn sót lại có thể gây ra hiện tượng mờ hoặc ăn mòn trên bề mặt lớp phủ.
Mẹo 7: Anodizing (chỉ dành cho các bộ phận bằng nhôm)
Anodizing là quá trình cốt lõi để cải thiện khả năng chống ăn mòn và hiệu ứng trang trí của các bộ phận kim loại tấm nhôm:
Điện áp khuyến nghị nên kiểm soát ở mức 10-20 V và thời gian xử lý được điều chỉnh theo nhu cầu (20-60 phút).
Nhuộm và phủ sau quá trình oxy hóa là những bước quan trọng để tăng cường khả năng chống oxy hóa và độ bền màu.
Công nghệ tiên tiến: Sử dụng công nghệ oxy hóa vi hồ quang (MAO) để cải thiện hơn nữa độ cứng và khả năng chống mài mòn của màng oxit.
Mẹo 8: Mài và đánh bóng bề mặt để cải thiện độ chính xác
Xử lý bề mặt chất lượng cao không thể tách rời khỏi quá trình mài và đánh bóng:
Lựa chọn giấy nhám: Từ thô đến mịn, từng bước một, ví dụ, trước tiên sử dụng loại giấy nhám 320#, sau đó chuyển sang loại lưới 800# hoặc cao hơn.
Vận hành nhất quán: Hướng mài phải nhất quán để tránh trầy xước ảnh hưởng đến hình thức.
Đối với các chi tiết có yêu cầu độ bóng cao, có thể sử dụng phương pháp đánh bóng gương, kết hợp với kem đánh bóng hoặc kem oxit crom để nâng cao hiệu quả.
Mẹo 9: Tăng cường kiểm tra chất lượng và kiểm soát quy trình
Sự ổn định của chất lượng xử lý bề mặt không thể tách rời khỏi việc kiểm tra và kiểm soát:
Máy đo độ dày lớp phủ: phát hiện độ dày lớp phủ.
Kiểm tra độ bám dính: chẳng hạn như kiểm tra cắt ngang hoặc kiểm tra kéo ra để xác minh xem lớp phủ có chắc chắn không.
Thử nghiệm phun muối: để đánh giá khả năng chống ăn mòn.
Đề xuất cải tiến: bằng cách đưa thiết bị kiểm tra tự động vào sử dụng, đảm bảo hiệu quả kiểm tra và kết hợp phân tích dữ liệu để tối ưu hóa quy trình theo thời gian thực.
Mẹo 10: Học tập liên tục và đổi mới công nghệ
Công nghệ xử lý bề mặt đang thay đổi từng ngày và để duy trì vị thế dẫn đầu về công nghệ đòi hỏi:
Chú ý đến xu hướng của ngành: nắm bắt các xu hướng quy trình mới nhất bằng cách tham gia các triển lãm và hội thảo.
Đầu tư nghiên cứu và phát triển công nghệ: giới thiệu các thiết bị thông minh và vật liệu mới thân thiện với môi trường để nâng cao hiệu quả và mức độ bảo vệ môi trường.
Ví dụ, các công nghệ mới nổi như lớp phủ nano và phun plasma đang dần được thúc đẩy, mang đến nhiều khả năng hơn cho lĩnh vực xử lý bề mặt.
Thời gian đăng: 06-12-2024